金属材料是现代应用最为广泛的重要工程材料。但是由于其自身的原因及其使用的环境介质的影响,难免要发生腐蚀、磨损等各种形式的损坏,降低了工件的使用寿命,造成了很大的经济损失。通过合金化和表面处理来提高金属材料的性能是材料科学工作者通常采用的办法。微弧氧化便是近十几年以来在阳极氧化的基础上发展起来的表面处理新技术。
微弧氧化(Microarc Oxidation)又称为微等离子体氧化(Micro PlasmaOxidation)或者阳极火花沉积(Anodic Spark Deposition),是将Ti,Al,Mg,Nb,Zr,Ta等金属及其合金置于处理液中,利用电化学方法,在热化学、等离子化学和电化学的共同作用下,生长出原位陶瓷的一种表面处理技术。该技术原位生成陶瓷膜的特点决定了其特别适合于对高速运动和耐磨耐蚀性能要求高的部件处理。现如今,材料科学工作者已经成功的对铝质材料(LY、LC、LD、ZL等)、镁、钛等材料及其合金表面应用微弧氧化技术制得了各种类型的陶瓷层,并对处理液、生长规律和生长机理等方面作了系统性的定量和定性分析,取得了一定的研究成果,在某些方面已经投入了实际的工程应用。但是,我们注意到,到目前为止,工程上应用量很大的钢材料还不能直接应用微弧氧化技术。而出自于使用中耐蚀、耐磨、减摩的需要,这些钢零件也渴望穿上一层陶瓷“外衣”,来提高使用寿命。
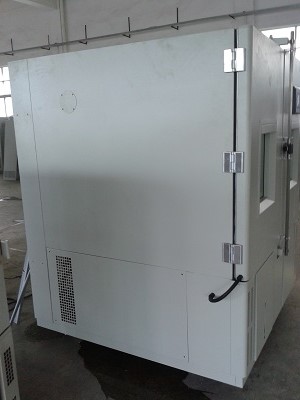
近些年来,钢表面等离子喷涂陶瓷、激光熔覆陶瓷和气相沉积陶瓷技术已经在某些领域应用,但是由于这些涂层不易进行后加工,或者对基体的热影响很大,有的因为造价过高等因素而难以推广。为了使微弧氧化技术应用于钢表面,我们想到了采用复合表面技术的方法来加以解决,即在钢表面先通过某种方式附着上一层能进行微弧氧化的材料后再进行微弧陶瓷化处理,我们称之为钢表面的复合陶瓷化,这样就相当于在钢表面生成了陶瓷层。关于采用这种方法在钢表面形成陶瓷层的研究目前尚未见其它报导。能进行微弧氧化的材质当中由于铝质材料相对来说易于获得,我们采用铝作为附着于钢表面进行微弧氧化的材料。本课题采用电弧喷涂的方法在零件需要处理的部分形成铝涂层,然后再进行微弧氧化。这样大大的拓宽了此项技术的应用范围,具有较高的实际工程应用价值。
但是这中间存在最突出的问题就是电弧喷涂铝涂层和钢基体之间还仅仅是机械结合,其结合强度还不能很好的适应实际工程应用的需要。因此,我们在喷涂之后、微弧氧化之前对涂层进行重熔处理,来提高涂层和基体之间的结合强度。常见的涂层重熔技术很多,如激光重熔、电子束重熔、氧-乙炔火焰重熔、整体加热重熔和感应重熔等。然而激光设备造价很高,氧-乙炔火焰重熔和整体重熔加热对工件的热影响区及变形都很大。感应重熔利用电磁感应的原理将电能转变成热能,在集肤效应的作用下,热量集中于涂层与基体界面,电磁搅拌作用还可以清除夹杂和气孔,此外,感应重熔可具有加热速度快,生产效率高的特点。根据各种重熔处理方法的特点、电弧喷涂铝涂层的特点以及涂层在处理后所要达到的具体要求,我们采用高频感应加热设备对涂层进行重熔处理。
本实验的进行将会扩大微弧氧化技术的应用范围,并对钢零件的修复、防蚀、耐磨等问题的解决具有实际意义。而且随着现代工业及科学技术的发展,陶瓷材料凭着其优异的性能将成为继钢、铝材等第二代工程材料以后的第三代工程材料,而本课题的研究将使第二代、第三代工程材料达到的结合,具有十分广阔的应用前景。(正航仪器编辑)
http://china-unin.com